Structural Components: Crossmembers
New Standard Corporation is a leading vertically integrated contract manufacturer in metal stamping, welding, fabrication, and high-complexity assembly. We also specialize in value-added solutions such as supply chain resilience and optimizing designs for manufacturability. These capabilities reduce costs and enhance the quality of the final product.
Below is a case study of one of our projects in the Class 8 truck industry that shows our commitment to going above and beyond for our customers. The project involved substantial investments in the refurbishment and automation of our older progressive stamping press allowing New Standard to meet our Customer’s tight tolerances.
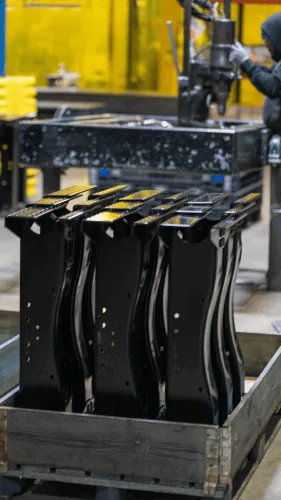
Ready To Start Your Next Project?
The Challenge: Quality Issues with Class 8 Truck Crossmembers
A customer came to us with persistent quality issues from their previous supplier. For their Class 8 trucks, they needed high-quality steel crossmembers, which are safety-critical parts. Their previous supplier’s process relied on manual labor, which is susceptible to human error, and lacked the precision needed to consistently meet quality standards.
Their manual riveting process was of particular concern because in manufacturing there is a certain sequence to riveting that must be followed—otherwise, the final product will not meet specifications. As such, the supplier kept delivering non-conforming crossmembers. Aware of New Standard’s manufacturing and engineering expertise, the client reached out to New Standard to produce their crossmembers moving forward.
At the time, we did not have and existing capabilities to produce crossmembers to the customer’s exact standards, so we engineered the process for this part. NSC invested over $1 million to completely revamp our existing stamping press, paint assemblies, and laser cutting. The plan was to transition the production process from hand-operated riveting to full automation. This meant we now had the ability to:
- Tighten quality control
- Improve product quality
- Scale production as needed
- Adapt to new designs down the road
The new parts would need to pass a ride handling test and shake test, which would be performed by the client.
The Solution: Automating Production Through Close Collaboration
Although neither New Standard and our customer had ever worked with an automated progressive stamping press on these specific parts, both teams were determined to engineer the specific process to produce the right part. We worked very closely with the customer, especially their product engineers, from initial design to production part approval process (PPAP) to production.
After upgrading our progressive stamping press, we automated the correct riveting sequence for all 24 rivets of the part, ensuring consistent high quality standards. We also integrated fail proof mechanisms directly into the riveting process, which would automatically stop the assembly if any issues were detected. NSC’s newly automated system produced crossmembers that met the client’s tolerance requirements.
Within a 10-week timeframe, we successfully implemented our automated solution, demonstrating our client-focused, problem solving, engineering, and risk mitigation capabilities. The new crossmembers passed the client’s ride, handling, and shake tests as well as rigorous standards set by GM, particularly regarding plating.
The Result: Producing 50,000 Crossmembers Per Year
New Standard is proud to share that our client no longer has any tolerance or quality issues. They said our crossmembers were the best they had received from any supplier. As a result of this success, we now produce 50,000 of these critical components annually, and we are looking to help more companies with their Class 8 truck crossmember production assemblies.
Our automated process gives OEMs more flexibility and fewer design requirements, making the transition from manual to automated production a seamless transition. Contact us today to learn how New Standard can engineer the right solution for your project.
Case Studies
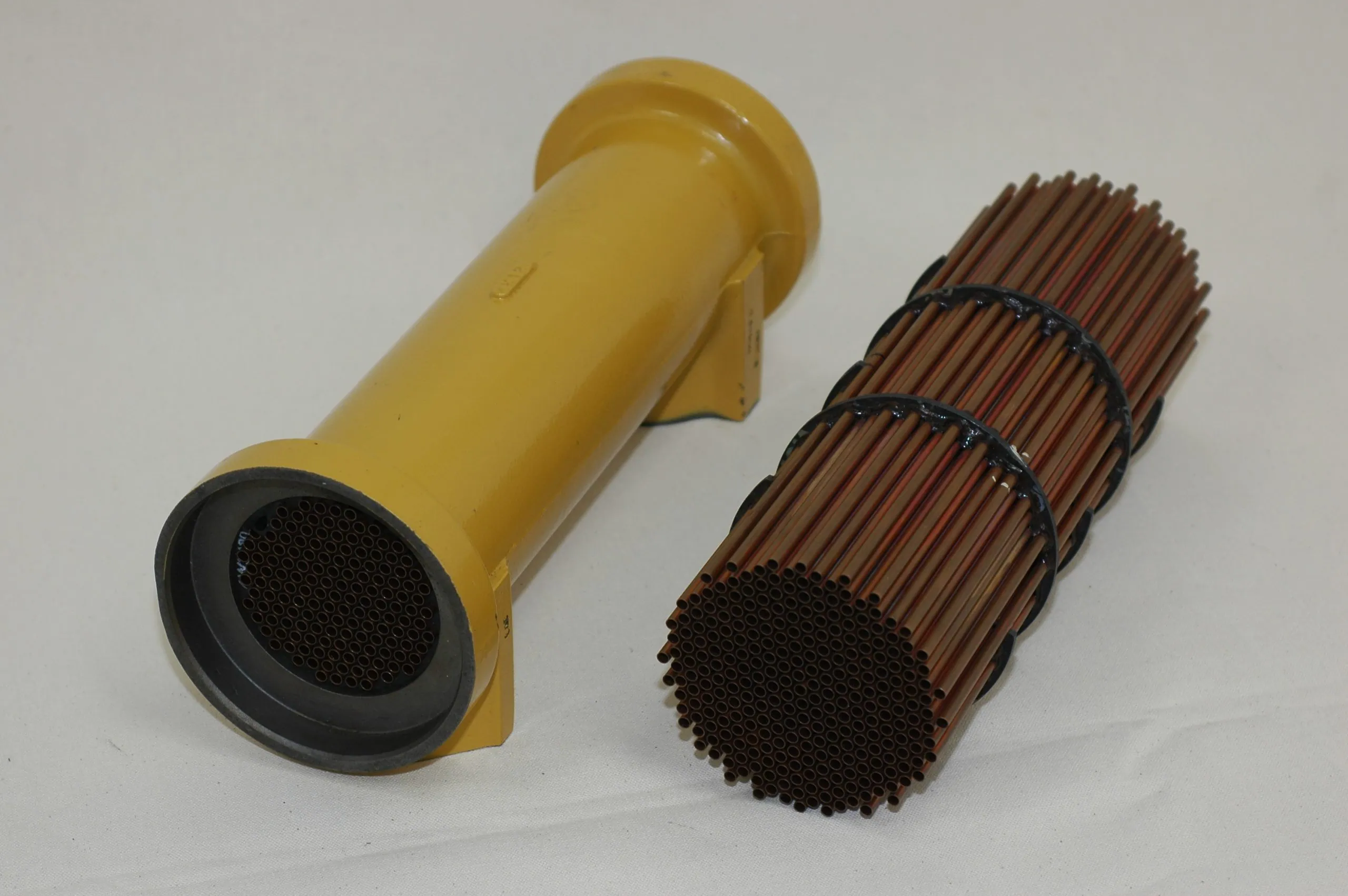
Oil Coolers
Learn how New Standard’s vertical integration and supply chain expertise helped an OEM increase output and quality for their oil coolers.
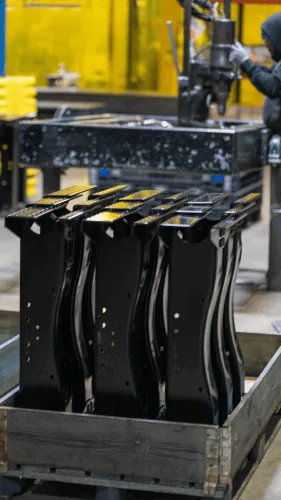
Crossmembers
Learn how New Standard helped a customer overcome previous supply chain issues to produce high-quality steel crossmembers for their Class 8 trucks.
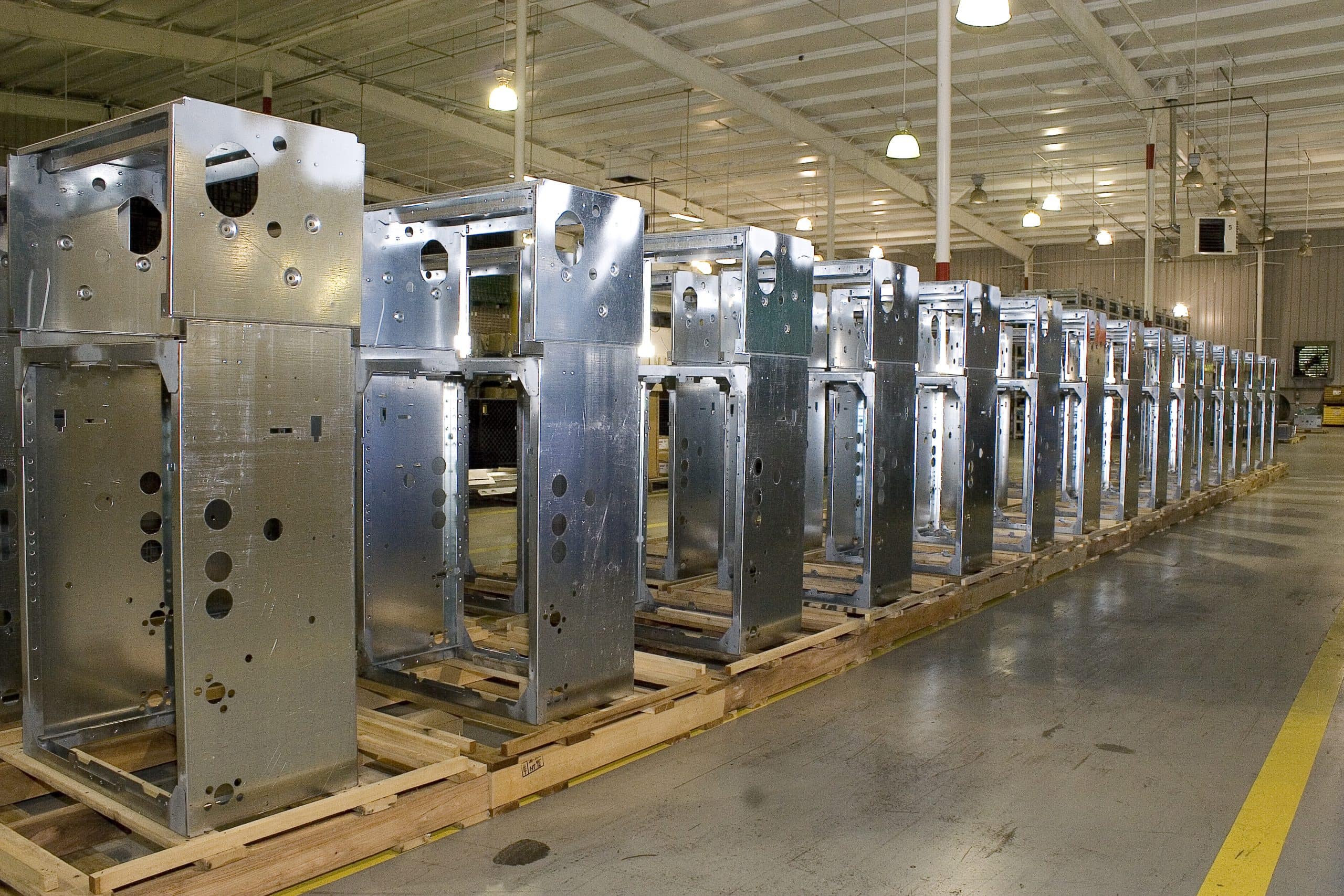
Fuel Dispenser Frames
New Standard provides diverse industries with optimized product solutions focused on design and cost improvement. Learn how we partnered with a long-time customer to develop new fuel dispenser frames.